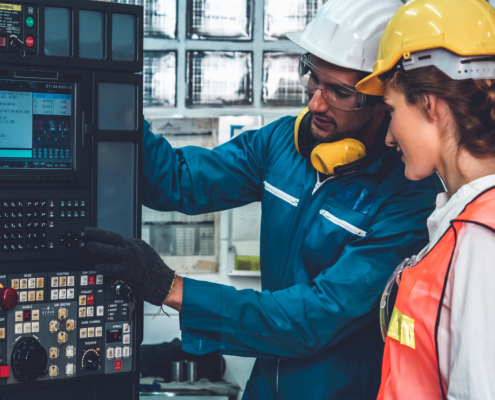
Maintaining a commercial plumbing system is crucial for the smooth operation of any business. A well-maintained plumbing system ensures the comfort of employees and customers and helps prevent costly repairs. This blog includes a comprehensive checklist for commercial plumbing maintenance, covering essential tasks to keep your plumbing system in top condition.
What to Include in a Commercial Plumbing Maintenance Checklist
Regular Inspections
The cornerstone of preventive maintenance for any commercial plumbing system is regular inspections. These help you detect issues before they escalate into costly repairs or severe damage to your plumbing.
When establishing an inspection schedule, it’s crucial to incorporate different levels of checkups:
- Annual Inspections: An in-depth look at the entire plumbing system should be conducted once a year. This includes water heaters, backflow devices, and boilers.
- Semi-Annual Inspections: Every six months, have your grease traps, sump pumps, and ejector pumps professionally examined.
- Monthly Checkups: More frequent visual inspections can detect leaks, corrosion, or clogs in high-traffic areas like restrooms and kitchens.
A detailed checklist for each type of inspection ensures that no component is overlooked and maintains a high standard of plumbing performance.
Drain Cleaning & Maintenance
Effective drain cleaning and maintenance are vital for any commercial plumbing system. Professional drain maintenance prevents inconvenient blockages and extends the lifespan of your plumbing infrastructure. Experts recommend that commercial drains should be thoroughly cleaned and inspected at least once or twice a year, depending on system usage and the nature of the business.
Blocked drains can lead to unpleasant odors, health hazards, and even property damage through water backups or flooding. Regular drain cleaning isn’t just about reacting to visible blockages, but about proactively addressing build-up that can accumulate and cause problems over time.
- Prevent Overflows: Routine cleaning helps prevent drain overflows and backups.
- Reduce Odors: Regular removal of debris and build-up eliminates unpleasant smells.
- Identify Problems Early: You can detect minor issues before they escalate into major repairs.
- Maintain Hygiene Standards: A clean drain fosters a healthier environment for staff and customers.
Faucet & Fixture Check-Ups
Proper functioning of faucets and fixtures is crucial in maintaining the integrity of commercial plumbing systems. Regular check-ups prevent water waste and identify areas requiring attention before they escalate into bigger issues. A comprehensive maintenance schedule for your faucets and fixtures enhances their longevity and ensures sustainable operations.
Inspecting & Maintaining Faucets & Fixtures
- Visual Inspection: Check for any signs of damage or corrosion. Pay close attention to handles, spouts, and the area around the base of the fixtures.
- Operational Testing: Test the operation of each faucet to make sure it turns on and off quickly and doesn’t drip after shutting off. The water flow should be even and steady.
- Seal & Washer Check: Check the seals and washers inside the faucets for damage—these are common culprits for leaks and drips.
- Aerator Maintenance: Replace or remove and clean faucet aerators to ensure a consistent flow rate and prevent clogs and mineral buildup.
Tips for Identifying Wear & Tear
Diligence is key in the early detection of wear and tear. Look for:
- Leaks and Drips: Persistent leaks and drips often indicate failing parts or the need for fixture replacement.
- Erratic Water Flow: Fluctuations in water flow or sprays indicate compromised internal mechanisms.
- Strange Noises: Unusual noises when operating the fixture could suggest an obstruction or a malfunction within the system.
- Signs of Corrosion: Rust or green patina on metal surfaces, particularly around connections, can significantly weaken the fixture and cause leaks.
Water Pressure Assessment
Maintaining optimal water pressure is critical to a plumbing system’s integrity. A commercial plumbing system must sustain a certain range of pressure levels to prevent undue stress on pipes, fixtures, and joints. Water pressure that’s too low can result in poor equipment performance and customer dissatisfaction, while pressure that’s too high risks leaks, burst pipes, and long-term infrastructure damage.
How to Accurately Measure & Adjust Water Pressure
A water pressure assessment is a multi-step process that should be conducted accurately and precisely. Professionals typically use the following methods:
- Gauge Testing: A pressure gauge is a tool that can be attached to various parts of the system, like a hose bib or a faucet, to provide an exact reading of the pressure (measured in pounds per square inch, or psi).
- Monitoring: Monitoring systems can be installed to track water pressure over time, identifying fluctuations that indicate underlying issues.
- Adjustment: If the water pressure is outside the acceptable range, usually 40–60 psi, a pressure-reducing valve (PRV) can be adjusted or installed to mitigate this issue.
Regular assessments and adjustments ensure a consistent supply of water and identify plumbing issues before they escalate. By incorporating a water pressure assessment into your plumbing maintenance checklist, you preserve the longevity of your infrastructure and ensure seamless operations.
Water Heater Service & Inspection
Commercial plumbing systems demand consistent monitoring and maintenance; an integral component of these systems is the water heater. Keeping your water heater in top condition provides consistent hot water, prevents costly breakdowns, and prolongs the unit’s lifespan. Here are some signs your water heater needs servicing:
Problems to Watch Out for in Water Heater Maintenance
- Temperature fluctuations: Inconsistent water temperatures can signal element or thermostat issues.
- Strange noises: Pops, bangs, or rumbling noises indicate sediment buildup that requires attention.
- Water discoloration: Rusty or murky water suggests corrosion inside the tank or pipes.
- Leaks: Water pooling around the heater is an immediate red flag for potential leakage.
- Age: Water heaters typically have a lifespan of 8–12 years. Aging units should be inspected regularly to gauge their condition.
The Importance of Regular Water Heater Inspections
Regular inspections are a cornerstone of preventive maintenance. They’re an opportunity to identify issues before they escalate into major problems. An expert inspection delves into system components, including the tank, valves, thermostats, electrical connections, and other critical areas. Detecting and addressing problems early on not only ensures a reliable supply of hot water, but contributes to operational efficiency and energy savings.
With SB Mechanical, you get comprehensive maintenance plans that safeguard your plumbing system. Learn more about our solutions.
Keep Your System in Peak Condition With Our Plumbing Maintenance Checklist
Smith-Boughan Mechanical understands the importance of keeping your plumbing system in peak condition. We maintain equipment and keep your working environment clean and safe. Our team has experience helping businesses across industries, including:
Contact us today to build your plumbing maintenance checklist.
Share This Post
More Like This
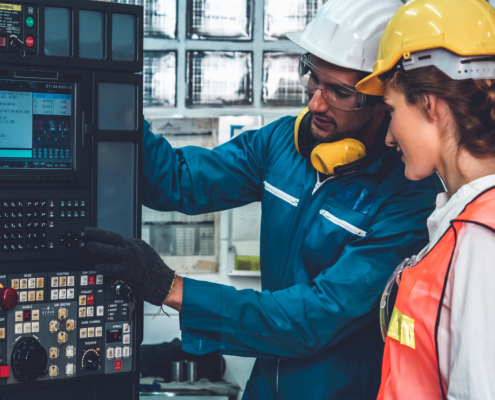
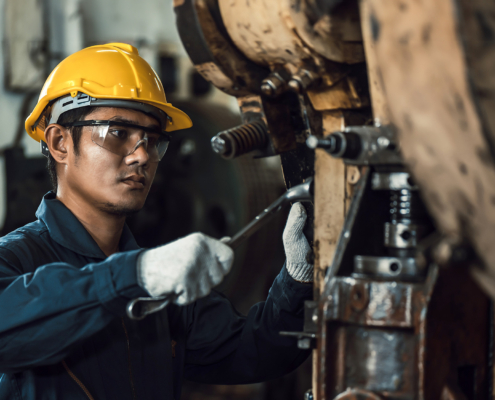
How to Develop a Quality Control Plan for Industrial Maintenance
Industrial Services (Quality Control), Maintenance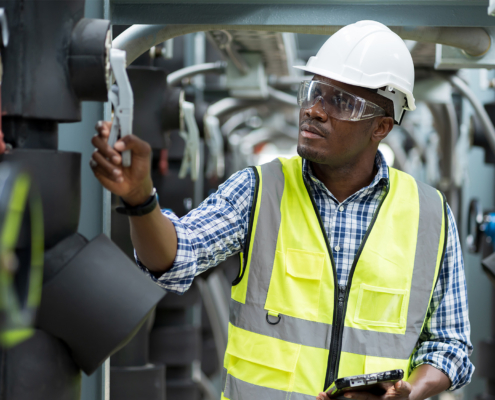
Understanding Industrial Maintenance Compliance Guidelines
Industrial Services (Maintenance), Maintenance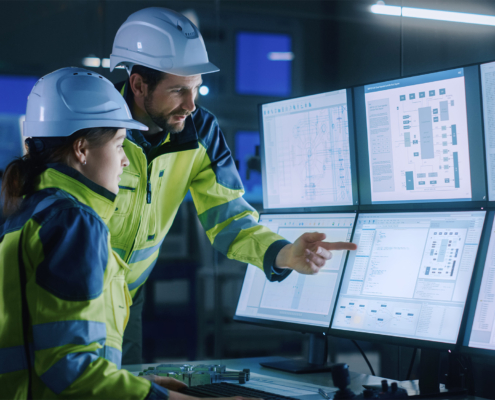
The Role of Technology in Industrial Maintenance Practice Innovations
Industrial Services (Maintenance), Maintenance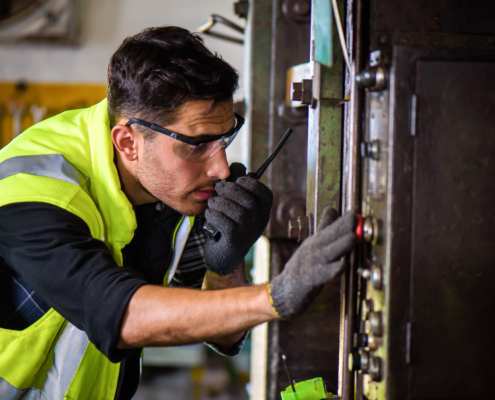
Factors to Consider When Choosing an Industrial Maintenance Provider
Industrial Services (Maintenance), Maintenance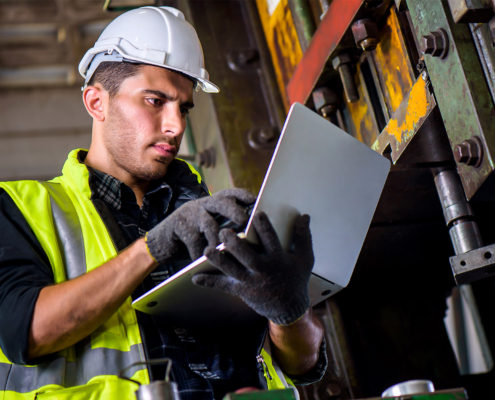
Best Practices for Improving Industrial Maintenance
Industrial Services (Maintenance), Maintenance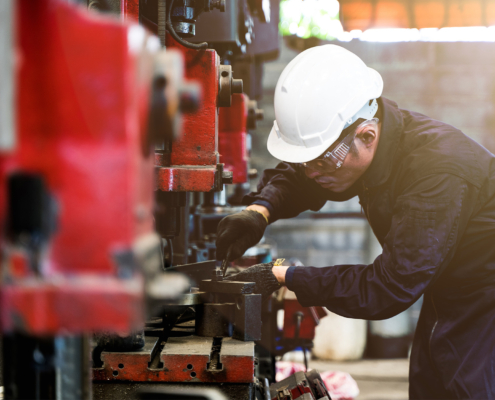
Exploring the Benefits of Routine Industrial Maintenance
Building Services (Maintenance Agreements), Maintenance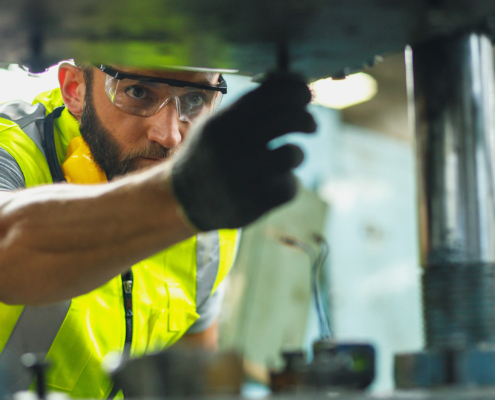
Your Guide to Industrial Maintenance
Building Services (Maintenance Agreements), Maintenance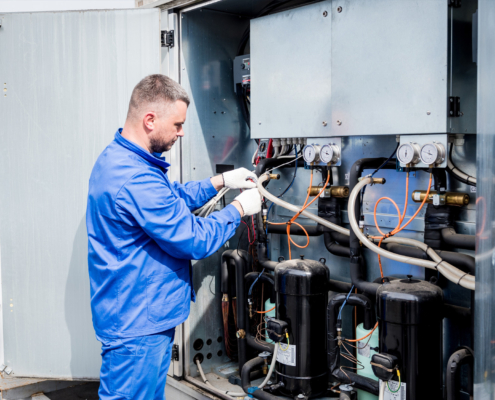
The Importance of a Commercial HVAC Maintenance Agreement
MaintenanceAbout Us
Smith-Boughan Mechanical has been servicing the Lima, Ohio, region with industry-leading mechanical design, fabrication, construction, and maintenance services since 1927.