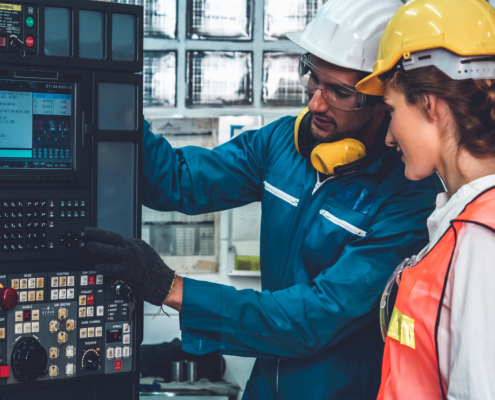
A plant shutdown or turnaround, whether for maintenance, upgrades, or other reasons, can be a critical period that demands meticulous planning and strategic execution. As we dive into the complexities of managing a plant shutdown, merging the shutdown schedule seamlessly with the broader production targets is essential to avoid costly downtime and productivity loss. Continue reading this article to learn proven strategies for a safe and efficient plant shutdown.
Understanding the Types of Plant Shutdowns
For a facility manager, the complexity of plant operations necessitates a clear understanding of the various types of plant shutdowns. Each type entails specific considerations and planning requirements. Let’s explore some of the common shutdown scenarios you might encounter.
Scheduled Maintenance Shutdowns
Scheduled plant maintenance shutdowns are preemptive measures to maintain and service equipment like HVAC, plumbing, and process systems, ensuring operational efficiency and safety. These shutdowns are planned based on equipment lifecycle and usage patterns. The foresight allows for minimal disruption, as activities are coordinated to optimize downtime with necessary repairs and updates.
Emergency Shutdowns
Unlike their scheduled counterparts, emergency shutdowns are reactionary. These plant shutdowns are often triggered by system failures, safety concerns, or unforeseen events that pose risks to plant personnel and infrastructure. The main priority is to swiftly halt operations to prevent accidents or damage, making this type of shutdown the most unpredictable and challenging to manage.
Seasonal Shutdowns
Seasonal shutdowns coincide with fluctuations in demand or external conditions that impact the operation. These can be strategically timed when decreased productivity is anticipated or to realign operations with market needs. Such shutdowns enable maintenance to be carried out without significant losses in production or profitability.
Turnaround Shutdowns
Turnaround shutdowns are extensive events, often involving large portions of a facility. They focus on significant overhauls, upgrades, and comprehensive inspections to enhance the plant’s performance or comply with technical advances and regulatory standards. The detailed and complex nature of turnarounds necessitates rigorous planning.
Financial Shutdowns
Financial shutdowns occur when economic circumstances dictate a temporary halt in operations. Market downturns, cost-cutting measures, or other financial constraints may drive these. The primary objective during such a shutdown is to preserve resources while strategies for fiscal recovery are explored.
Understanding the distinctions between these types of shutdowns affords facility managers the perspective needed to approach each situation with tailored strategies that mitigate risks, control costs, and maintain compliance.
The Step-By-Step Process for a Plant Shutdown
Effectively managing a plant shutdown is critical to ensuring minimal disruption, maintaining safety standards, and securing equipment integrity. From initial planning to the final review stage, each step requires meticulous attention. Here’s a structured approach to a successful plant shutdown.
Scope the Project
Scoping the project is the preliminary stage, where you establish the extent and aims of the shutdown. It involves:
- Identifying the objectives of the shutdown.
- Determining the tasks that need to be completed.
- Assessing resource requirements, including personnel and materials.
- Creating a timeline for the shutdown.
Prepare
Preparation is vital to a seamless plant shutdown. This stage should cover:
- Finalizing shutdown schedules and communicating them to all stakeholders.
- Ensuring all necessary resources, including spare parts and machinery, are on hand.
- Training the shutdown team on their roles and safety procedures.
- Performing a detailed risk assessment and implementing mitigation strategies.
Execution
The execution phase is the core of the plant shutdown. Focused and efficient work during this period entails:
- Following the predefined schedule to avoid unnecessary delays.
- Maintaining clear communication channels throughout the team.
- Monitoring safety practices rigorously to protect workers and equipment.
- Documenting the progress and any issues encountered for real-time adjustment and future reference.
Start-Up
After maintenance tasks are completed, the focus shifts to starting up the plant. The start-up process typically involves:
- Inspections to ensure that work has been completed to the required standards.
- Gradual equipment testing to confirm operational readiness.
- Recommissioning systems and processes according to agreed protocols.
- Continuous monitoring for any issues as operations resume.
Review
Post-shutdown, it is important to review the entire process. The review aims to:
- Analyze the outcomes versus the initial objectives.
- Examine the efficiency of the shutdown and identify areas for improvement.
- Document lessons learned and integrate this knowledge into future shutdown plans.
- Validate that the plant is fully operational and meeting performance expectations.
A comprehensive understanding and careful execution of these steps can vastly improve the efficiency and safety of your plant’s shutdown and start-up procedures.
Essential Duties Associated With Plant Shutdowns
Managing a plant shutdown requires in-depth knowledge and precise execution of several critical duties. As a facility manager, you oversee these tasks and ensure they are performed safely, efficiently, and effectively. The complex nature of the work makes it imperative to have an exhaustive checklist of tasks at hand, which typically include:
- Conducting a thorough review of shutdown procedures and safety protocols.
- Ensuring that all equipment is properly powered down and secured.
- Coordinating with the maintenance team for equipment inspections and repairs.
- Managing inventory and ensuring that necessary spare parts are available.
- Predictive maintenance integration to foresee potential issues before they arise.
- Overseeing the clean-up of the facility to ensure it is ready for reopening.
Predictive Maintenance Integration
Among these duties, the integration of predictive maintenance stands out as a forward-thinking strategy. Predictive maintenance helps to:
- Identify potential equipment failures before they occur.
- Minimize the downtime by planning repairs during the shutdown.
- Reduce the costs associated with unexpected breakdowns.
- Extend the life of machinery by preventing wear and tear.
Structuring Your Shutdown Team: Organization and Roles
Ensuring a successful plant shutdown hinges on the team charged with its management. A precise understanding of each team member’s role and a balanced mix of internal and external expertise is vital for efficient and effective job execution. Below, we explore the critical components of organizing a robust shutdown team structure.
Key Roles for Effective Job Execution
It cannot be overstated how important it is to create a well-defined hierarchy of roles within the shutdown team. Key personnel must be identified early, with clear expectations and responsibilities delineated. This often includes project managers, safety officers, maintenance supervisors, and quality control inspectors. Such a hierarchy ensures that every aspect of the shutdown is overseen by qualified individuals, creating a streamlined and accountable framework.
Balancing In-House Talent with External Expertise
Utilizing a combination of in-house employees and external professionals can bring the best balance of familiarity and specialized knowledge to the project. The enternal staff possess a deep understanding of the plant’s systems and processes, whereas external experts can provide a fresh perspective and specialized skills that might not be available internally. The key is to integrate these resources cohesively, avoiding jurisdictional overlaps that could lead to confusion or inefficiency.
Facility Manager‘s Manager’s Role in Team Leadership and Support
The facility manager operates at the helm of the shutdown operation. They play a critical role in providing leadership and support to the team. As the linchpin of the shutdown process, the manager must ensure consistent communication, resource availability, and morale maintenance. Their leadership is crucial in enforcing safety standards, delivering efficiency that adheres to budget constraints, validating that all shutdown activities are performed to the highest quality standards, and having a contingency plan if something goes wrong.
- Leadership: Guiding the team towards common goals and ensuring adherence to the shutdown schedule.
- Support: Offering the necessary resources and addressing potential bottlenecks impacting timelines or quality.
- Communication: Keeping all stakeholders informed and aligned on shutdown progress and any arising issues.
- Safety and Quality: Upholding the highest safety standards and ensuring project deliverables meet quality expectations.
Ensure an Efficient and Effective Plant Shutdown With the Help of Smith-Boughan
Since 1927, Smith-Boughan has proudly served our home community of West Central, Ohio, with exceptional design, fabrication, construction, and maintenance services, including plant shutdowns. If you have to halt operations for any reason, we’re here to help. Contact us today to schedule a time for us to discuss your shutdown and begin crafting a customized strategy for your plant.
Share This Post
More Like This
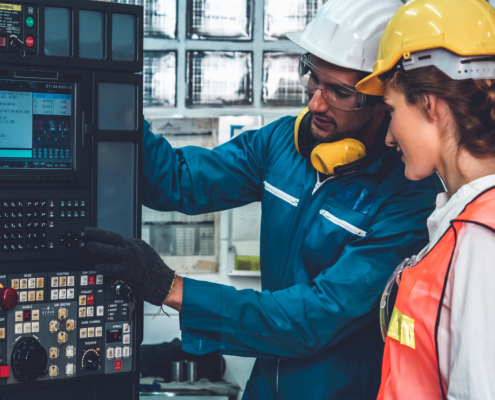
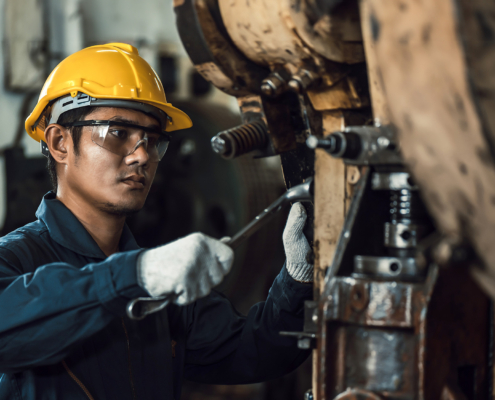
How to Develop a Quality Control Plan for Industrial Maintenance
Industrial Services (Quality Control), Maintenance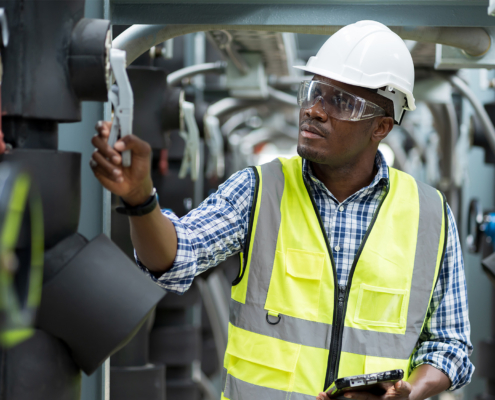
Understanding Industrial Maintenance Compliance Guidelines
Industrial Services (Maintenance), Maintenance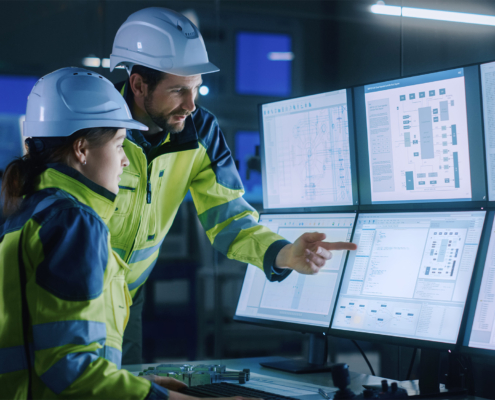
The Role of Technology in Industrial Maintenance Practice Innovations
Industrial Services (Maintenance), Maintenance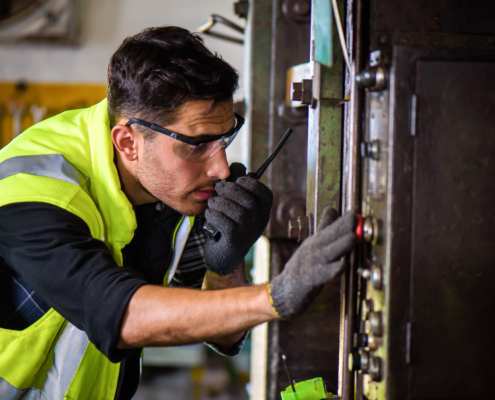
Factors to Consider When Choosing an Industrial Maintenance Provider
Industrial Services (Maintenance), Maintenance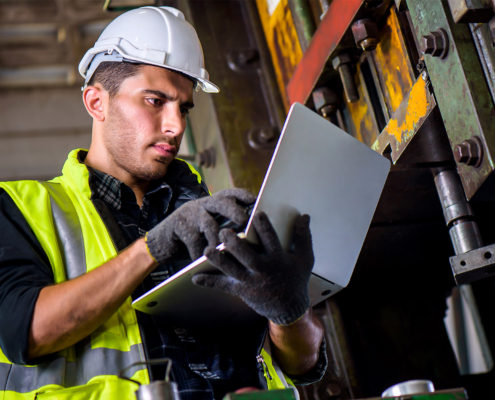
Best Practices for Improving Industrial Maintenance
Industrial Services (Maintenance), Maintenance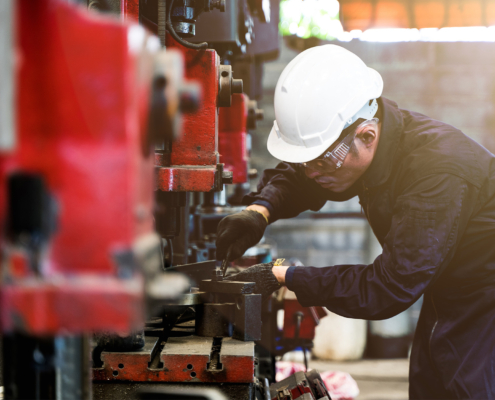
Exploring the Benefits of Routine Industrial Maintenance
Building Services (Maintenance Agreements), Maintenance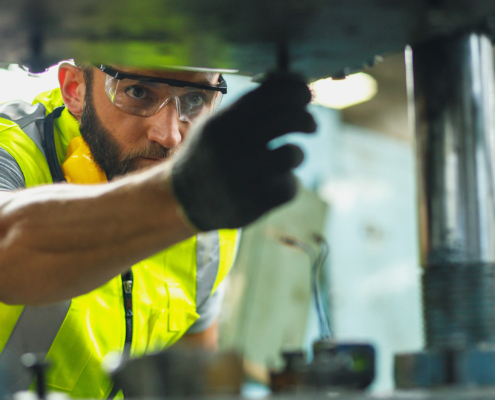
Your Guide to Industrial Maintenance
Building Services (Maintenance Agreements), Maintenance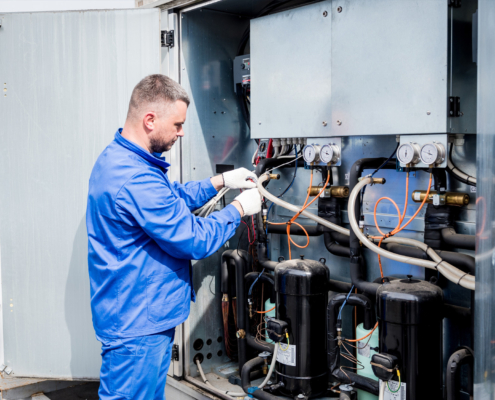
The Importance of a Commercial HVAC Maintenance Agreement
MaintenanceAbout Us
Smith-Boughan Mechanical has been servicing the Lima, Ohio, region with industry-leading mechanical design, fabrication, construction, and maintenance services since 1927.