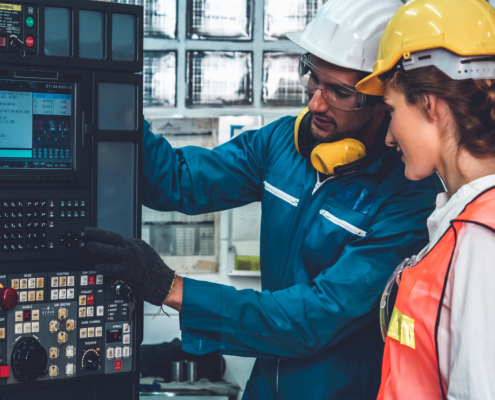
Industrial maintenance is a crucial aspect of ensuring the smooth and efficient operation of various industries. It includes a wide range of activities to maintain equipment, machinery, and facilities to prevent breakdowns and ensure optimal performance. This blog will explore what industrial maintenance involves, best practices for improving it, and the industries that rely on it the most.
What Is Involved in Industrial Maintenance?
Industrial maintenance involves several strategies and activities to keep equipment and machinery running smoothly. These strategies can be categorized into different types of maintenance, each with its unique approach and benefits.
Preventive Maintenance
Preventive maintenance is a proactive approach involving regular inspections, servicing, and equipment repairs before any failures occur. This type of maintenance is scheduled based on time or usage intervals and aims to identify and address potential issues before they lead to significant problems.
For instance, routine oil changes, filter replacements, and system checks are part of preventive maintenance. This approach not only extends the lifespan of equipment but also improves safety and reduces unexpected downtime.
Run-to-Failure Maintenance
Run-to-failure maintenance, also known as reactive maintenance, is a strategy where equipment is allowed to operate until it breaks down. Repairs or replacements are then carried out.
While this approach can be cost-effective for non-critical machinery, it can lead to unplanned downtime and higher repair costs for essential equipment. This strategy is typically used when the cost of downtime is lower than the cost of preventive measures or when the machinery is non-essential and its failure does not significantly impact overall operations.
Condition-Based Maintenance
Condition-based maintenance relies on monitoring the actual condition of equipment to determine the need for maintenance. This approach uses various sensors and diagnostic tools to collect data on equipment performance and health, allowing maintenance to be performed only when necessary, thus reducing unnecessary interventions.
Vibration analysis, thermography, and oil analysis are common techniques for monitoring machinery’s condition. By addressing issues based on real-time data, condition-based maintenance can optimize maintenance schedules and resources.
Predictive Maintenance
Predictive maintenance takes condition-based maintenance a step further by using advanced analytics and machine learning algorithms to predict when equipment will likely fail. By analyzing historical data and real-time inputs, predictive maintenance can forecast potential issues and schedule maintenance activities proactively, minimizing downtime and extending the life of the equipment. Techniques such as machine learning and artificial intelligence help in identify patterns and anomalies that might not be apparent through traditional monitoring methods.
Prescriptive Maintenance
Prescriptive maintenance uses predictive analytics and artificial intelligence to predict failures and recommend specific actions to prevent them. This approach provides detailed instructions on what maintenance activities should be performed, when they should be done, and how they should be executed, ensuring optimal maintenance efficiency.
For example, if a piece of equipment shows signs of potential failure, the system might recommend replacing specific components, adjusting operational parameters, or performing targeted maintenance to prevent a breakdown.
Smith-Boughan provides robust industrial maintenance and services solutions that ensure your equipment is always running at its best.
Best Practices for Improving Industrial Maintenance
Implementing best practices in industrial maintenance can significantly enhance the reliability and performance of equipment and machinery. Here are some key strategies to consider:
Proactive Maintenance Program
A proactive maintenance program focuses on anticipating and addressing potential issues before they become serious problems. This typically involves regular inspections, routine servicing, and timely repairs to prevent unexpected breakdowns.
By adopting a proactive approach, companies can reduce downtime, extend equipment lifespan, and improve operational efficiency. Proactive maintenance also includes training staff to recognize signs of wear and tear and ensuring they have the necessary skills to perform maintenance tasks effectively.
Using Mobile Maintenance Software
Mobile maintenance software enables maintenance teams to access and update maintenance information in real-time, regardless of their location. This technology streamlines communication, improves data accuracy, and enhances coordination among team members.
With mobile maintenance software, maintenance tasks can be tracked more efficiently, and response times to issues can be significantly reduced. The software also allows for easy documentation of maintenance activities, helping organizations maintain comprehensive records and ensure compliance with industry standards.
Defining Clear Procedures
Establishing clear and standardized maintenance procedures ensures consistency and quality in maintenance activities. These procedures should include detailed instructions on performing various maintenance tasks, safety protocols, and guidelines for reporting and documenting maintenance work. Clear procedures help reduce errors, improve compliance with regulatory requirements, and ensure that maintenance activities are carried out effectively.
Additionally, well-documented procedures facilitate training new staff and ensure continuity in maintenance practices even when personnel changes occur.
Setting, Measuring, and Improving Upon Goals
Setting specific, measurable, achievable, relevant, and time-bound (SMART) goals for maintenance activities is crucial for continuous improvement. Maintenance teams should regularly track their performance against these goals and identify areas for improvement. By analyzing key performance indicators (KPIs), such as mean time between failures (MTBF) and mean time to repair (MTTR), companies can make data-driven decisions to enhance their maintenance processes and achieve better results. Regularly reviewing and updating goals based on performance metrics ensures that maintenance practices evolve and improve over time.
Industries That Rely on Industrial Maintenance
Several industries depend heavily on industrial maintenance to ensure the reliability and efficiency of their operations. Here are some of the key sectors that rely on industrial maintenance the most:
Manufacturing
In the manufacturing industry, industrial maintenance is vital for keeping production lines running smoothly and minimizing downtime. Regular maintenance of machinery and equipment helps prevent costly breakdowns, improves product quality, and enhances overall productivity. Manufacturing facilities often use a combination of preventive, predictive, and condition-based maintenance strategies to ensure continuous operation and maintain high quality and safety standards.
Energy
The energy sector, including oil, gas, mining, and electric utilities, relies on industrial maintenance to ensure the safe and efficient operation of critical infrastructure. Maintenance activities in this industry involve:
- Regular inspections.
- Servicing of pumps and turbines.
- Monitoring of pipelines.
- Maintenance of electrical systems to prevent outages and ensure continuous energy supply.
In this sector, predictive and prescriptive maintenance are particularly valuable for preventing catastrophic failures and ensuring compliance with stringent safety regulations.
Construction
The construction industry depends on industrial maintenance to keep heavy machinery and equipment in optimal working condition. Regular maintenance of cranes, excavators, bulldozers, and other construction equipment is essential for ensuring safety, reducing downtime, and completing projects on schedule. Maintenance practices in construction often include condition-based and preventive maintenance to address the harsh operating conditions and demanding usage patterns of construction machinery.
Aviation
In the aviation industry, industrial maintenance is crucial for ensuring the safety and reliability of aircraft. This involves routine inspections, servicing of engines and avionics systems, and adherence to stringent maintenance schedules to prevent failures and ensure the safety of passengers and crew. The aviation industry relies heavily on predictive and prescriptive maintenance to maintain the highest safety and efficiency standards, using advanced diagnostic tools and data analytics to monitor aircraft health.
Automotive
The automotive industry relies on industrial maintenance to keep production lines and manufacturing equipment running smoothly. Regular maintenance of robotic assembly lines, paint booths, and testing equipment helps ensure consistent product quality and reduces production delays. In the automotive sector, preventive, predictive, and condition-based maintenance are used to manage complex and highly automated production processes.
Find Your Industrial Maintenance Solution With Smith-Boughan
Smith-Boughan provides expert maintenance solutions for HVAC, piping, controls, energy management, and more. Our comprehensive services ensure your industrial facility remains safe, efficient, and productive. With our team of skilled professionals and advanced maintenance strategies, we help you minimize downtime, extend equipment lifespan, and enhance overall operational performance. Trust Smith-Boughan to deliver reliable and effective industrial maintenance solutions tailored to your needs.
Share This Post
More Like This
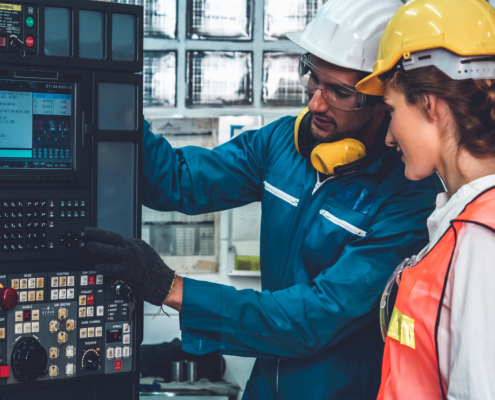
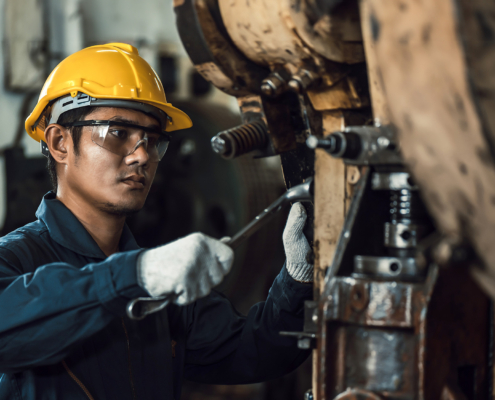
How to Develop a Quality Control Plan for Industrial Maintenance
Industrial Services (Quality Control), Maintenance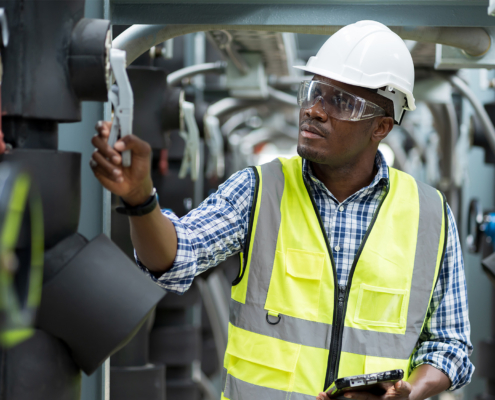
Understanding Industrial Maintenance Compliance Guidelines
Industrial Services (Maintenance), Maintenance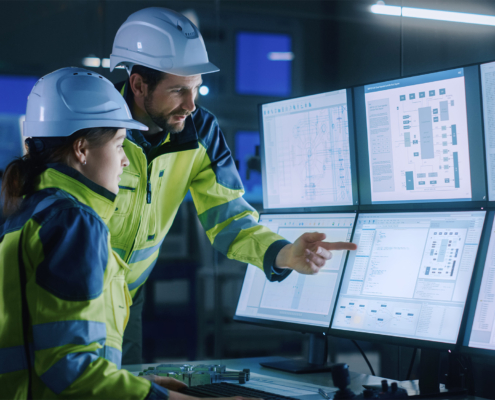
The Role of Technology in Industrial Maintenance Practice Innovations
Industrial Services (Maintenance), Maintenance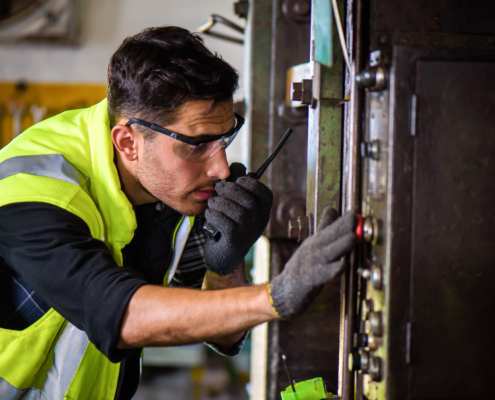
Factors to Consider When Choosing an Industrial Maintenance Provider
Industrial Services (Maintenance), Maintenance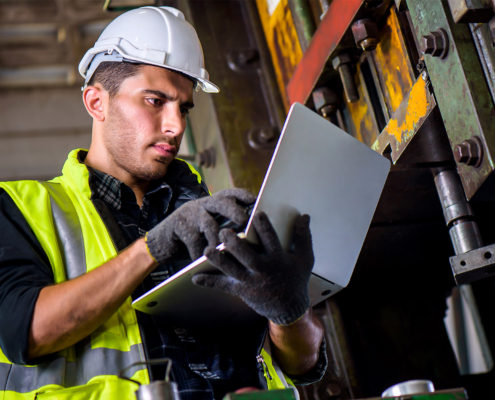
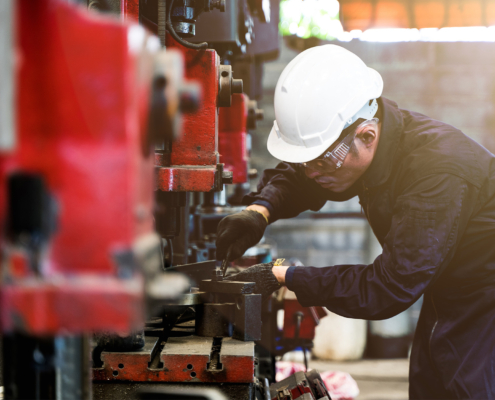
Exploring the Benefits of Routine Industrial Maintenance
Building Services (Maintenance Agreements), Maintenance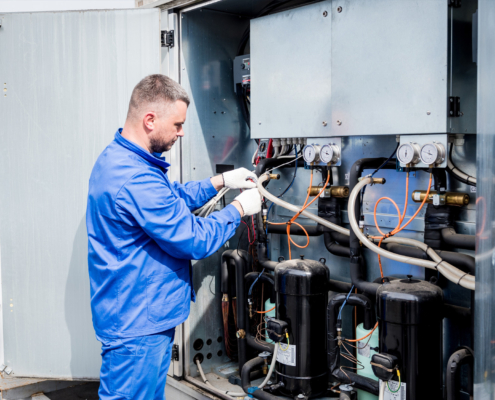
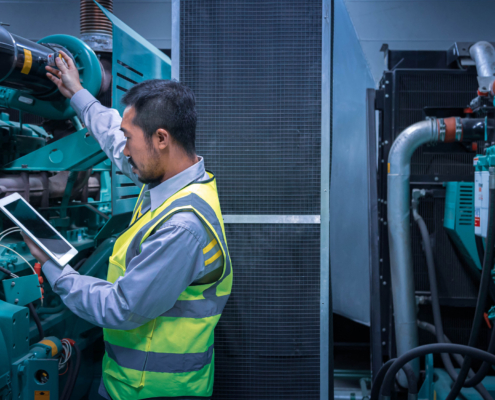
About Us
Smith-Boughan Mechanical has been servicing the Lima, Ohio, region with industry-leading mechanical design, fabrication, construction, and maintenance services since 1927.