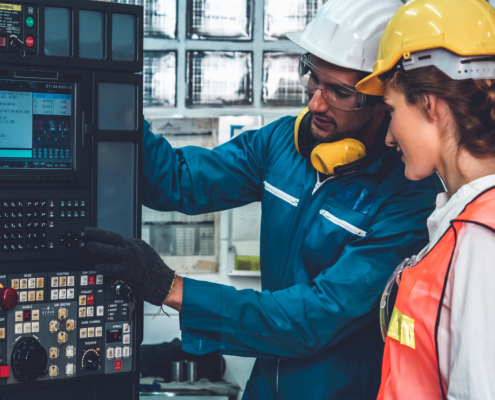
Ensuring the longevity and efficiency of industrial equipment is crucial for operational success. A robust quality control plan is essential to achieving this, as it provides a structured approach to maintaining high standards and minimizing downtime. By developing a comprehensive quality control plan, industrial facilities can proactively address maintenance challenges, enhance safety, and optimize performance.
In this blog, we’ll explore the key steps and strategies for creating an effective quality control plan tailored specifically for industrial maintenance.
The Importance of a Proper Quality Control Plan
Establishing a proper quality control plan for industrial maintenance is essential for ensuring that all equipment and processes operate at peak efficiency, minimizing downtime and costly repairs. A well-structured quality control plan—like Smith-Boughan’s comprehensive program—helps maintain compliance with industry regulations, ensuring that safety standards are met and reducing the risk of accidents. It also enhances overall productivity by identifying and addressing potential issues before they escalate into major problems.
A proper quality control plan sets clear expectations, standardizes procedures, and incorporates regular inspections, serving as a foundation for consistent, high-quality outcomes in industrial maintenance.
Developing a Quality Control Plan: Step-By-Step
Establishing a quality control plan for industrial maintenance requires a systematic approach to ensure that all aspects of the operation meet the highest standards. By following these steps, industrial facilities can enhance their maintenance procedures and ensure long-term operational success.
Step 1. Evaluate Existing Maintenance Procedures
Start by thoroughly evaluating current maintenance procedures. This step involves assessing the effectiveness, efficiency, and consistency of existing practices to identify strengths and areas needing improvement. Gathering data from maintenance logs, employee feedback, and performance metrics can provide a clear picture of where the facility stands. This foundational analysis is crucial for creating a quality control plan that addresses specific challenges and leverages existing strengths.
Step 2. Identify Objectives and Scope of the Plan
Once the existing procedures are evaluated, the next step is to define clear objectives and the scope of the quality control plan. These objectives should align with both regulatory requirements and the facility’s operational goals. Consider what outcomes are desired, such as improved safety, enhanced efficiency, or reduced downtime, and determine the specific areas of maintenance that the plan will cover. Establishing these parameters early on ensures that the plan is focused and actionable.
Step 3. Create SOPs
Develop comprehensive and standardized Standard Operating Procedures (SOPs) for all maintenance activities. SOPs provide detailed, step-by-step instructions for each task, ensuring consistency and accuracy in execution. Standardizing these procedures eliminates variability that can lead to errors or inconsistencies, thereby enhancing overall quality control. These SOPs should be easily understood, accessible to all relevant personnel, and regularly updated to reflect the latest best practices and technological advancements.
Step 4. Implement Regular Training Programs
Ongoing training is essential for maintaining high standards in industrial maintenance. Implement regular training programs to keep maintenance staff up-to-date with the latest techniques, technologies, and safety protocols. Continuous education ensures that all personnel are proficient in their roles and can adapt to changes in procedures or equipment. This commitment to training fosters a culture of continuous improvement, where quality control is a shared responsibility among all team members.
Step 5. Integrate Tech and Tools
Leverage technology and tools to enhance the effectiveness of your quality control plan. Integrating a Computerized Maintenance Management System (CMMS) can streamline maintenance tasks, track performance metrics, and schedule predictive maintenance. Predictive maintenance tools, such as IoT sensors and data analytics, can forecast potential issues before they become critical, reducing downtime and improving efficiency. Utilizing advanced technology ensures that your quality control efforts are proactive and data-driven.
Step 6. Conduct Routine Inspections and Audits
Hiring a professional like Smith-Boughan for regular inspections, audits, and performance metric checks is vital for maintaining the effectiveness of the quality control plan. These activities help identify any deviations from established standards and provide opportunities for corrective action before issues escalate. Routine assessments also offer insights into the plan’s performance, enabling continuous improvement. By systematically evaluating maintenance activities, you can ensure that quality control measures remain robust and effective.
Step 7. Periodically Review and Revise the Quality Control Plan
The final step in developing a quality control plan is to periodically review and revise it. As industrial environments evolve, so too should your quality control strategies. Regularly revisiting the plan allows you to incorporate new technologies, respond to changing regulations, and address any emerging challenges. This ongoing process of evaluation and adaptation ensures that your quality control plan remains relevant and effective in maintaining high standards across your facility.
Discover how Smith-Boughan’s industrial quality control maintenance program ensures the reliability, safety, and efficiency of your equipment.
Overcoming Common Challenges of Developing a Quality Control Plan
Developing a quality control plan for industrial maintenance can be complex, often accompanied by several challenges. However, understanding these challenges and implementing effective strategies to overcome them can help ensure the success and effectiveness of your quality control plan.
Let’s explore some of the most common obstacles faced during this process and how to address them effectively.
Resistance to Change
Implementing a new quality control plan may face resistance from staff accustomed to existing procedures. To overcome this, it’s crucial to involve employees early in the planning process, communicate the benefits clearly, and provide training to ensure everyone understands the new system’s importance and advantages.
Insufficient Resources
A lack of resources, such as time, budget, or personnel, can hinder the development and implementation of a robust quality control plan. Overcome this challenge by prioritizing critical areas of maintenance first, seeking management support for necessary resources, and exploring cost-effective technologies that can streamline the process.
Ensuring Consistent Compliance
Maintaining consistent compliance with industry standards and regulations can be challenging, especially in dynamic operational environments. To address this, integrate automated compliance tracking tools within your quality control plan, and schedule regular audits and reviews to ensure ongoing adherence to regulations.
Integrating Technology Effectively
The integration of advanced technology into your quality control plan may be complex due to compatibility issues or a lack of technical expertise. Overcome this by selecting user-friendly tools, providing thorough training for your team, and working closely with technology providers to ensure seamless integration and support.
Balancing Thoroughness with Efficiency
Striking a balance between comprehensive quality control measures and maintaining operational efficiency can be challenging. To address this, develop detailed yet efficient standardized operating procedures (SOPs) and regularly review them to eliminate unnecessary steps without compromising on quality.
Continuous Improvement and Adaptation
The industrial environment is constantly evolving, making it difficult to keep the quality control plan up to date. To overcome this, establish a culture of continuous improvement where feedback is regularly gathered and the plan is reviewed and adjusted as needed to stay aligned with industry advancements and operational changes.
To overcome these obstacles and create a quality control plan you can count on, turn to the professionals at Smith-Boughan, Inc.
Undergo Industrial Maintenance Planning With Smith-Boughan
At Smith-Boughan, we recognize the critical role that industrial maintenance planning plays in maintaining quality control. Our team understands how essential it is to ensure compliance, safety, and equipment efficiency within your facility. By partnering with us, you can develop a tailored quality control plan that aligns with your operational goals.
Let us help you maintain the highest standards in industrial maintenance, ensuring your facility runs smoothly and efficiently while staying compliant with industry regulations. Contact us today to get started.
Share This Post
More Like This
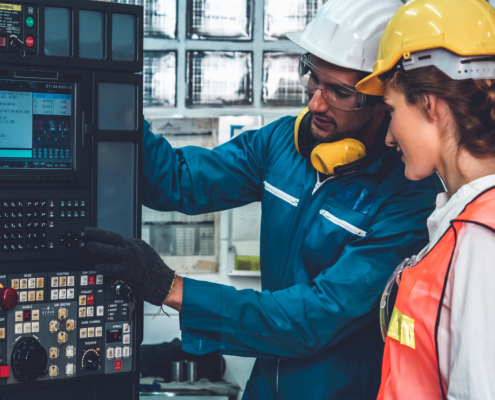
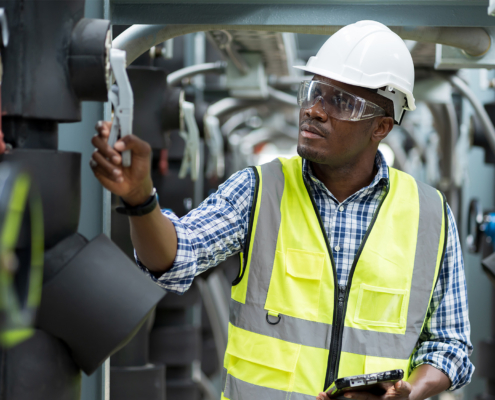
Understanding Industrial Maintenance Compliance Guidelines
Industrial Services (Maintenance), Maintenance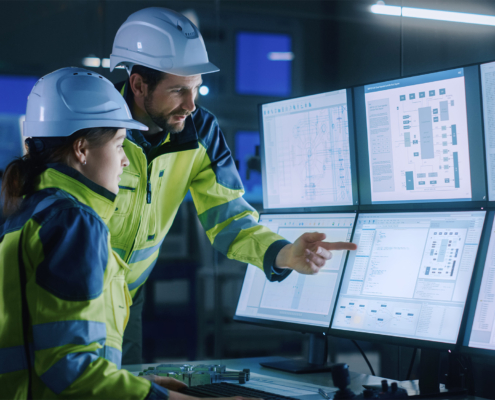
The Role of Technology in Industrial Maintenance Practice Innovations
Industrial Services (Maintenance), Maintenance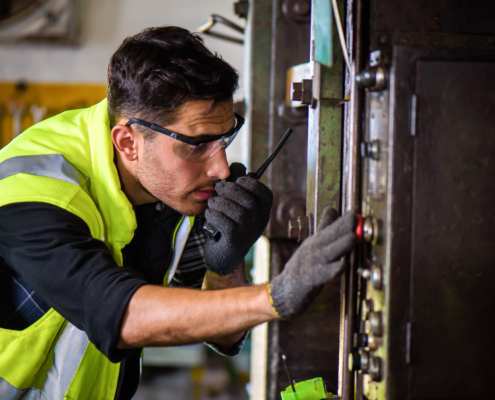
Factors to Consider When Choosing an Industrial Maintenance Provider
Industrial Services (Maintenance), Maintenance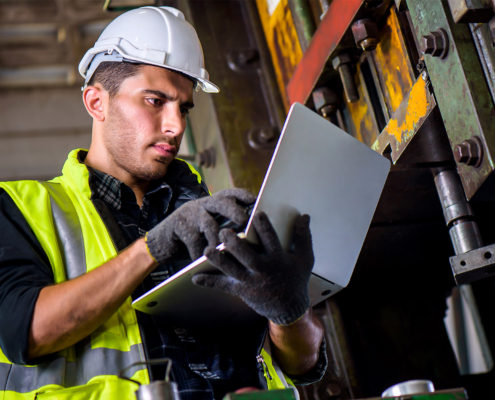
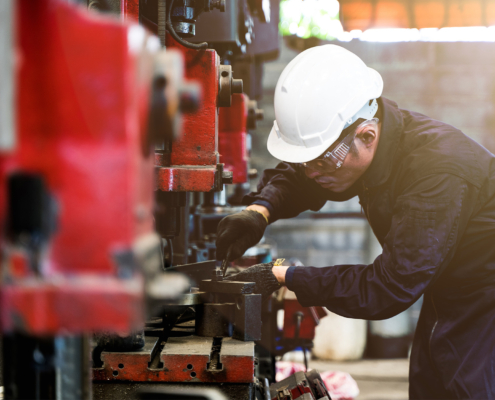
Exploring the Benefits of Routine Industrial Maintenance
Building Services (Maintenance Agreements), Maintenance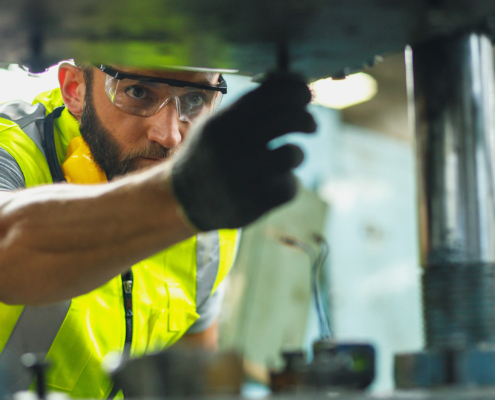
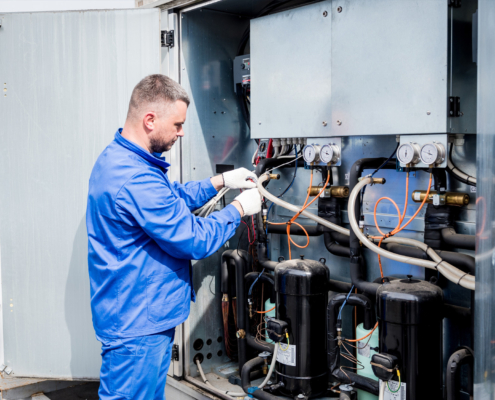
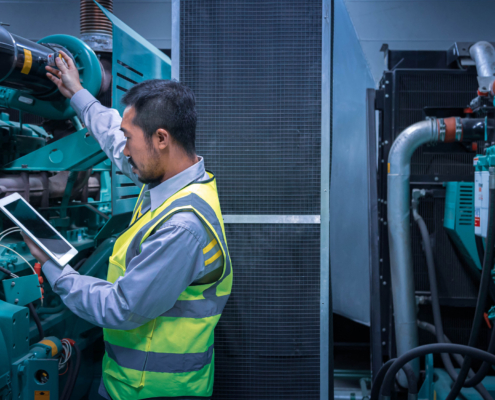
About Us
Smith-Boughan Mechanical has been servicing the Lima, Ohio, region with industry-leading mechanical design, fabrication, construction, and maintenance services since 1927.