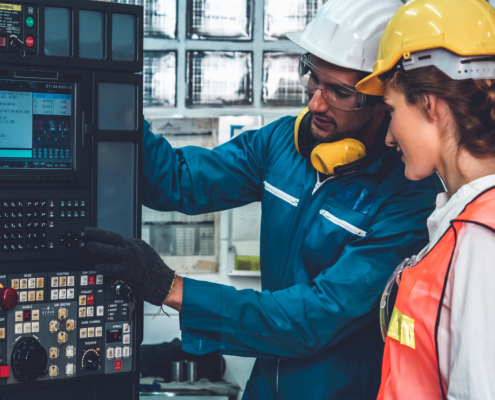
Efficient industrial maintenance is essential for minimizing downtime, extending equipment life, and reducing costs. Plant managers who adopt best practices can ensure their maintenance teams—whether in-house or outsourced—always operate at peak efficiency.
Here are some best practices for improving industrial maintenance.
Proactive Maintenance Programs
A proactive maintenance program is the cornerstone of efficient industrial maintenance. By focusing on preventative rather than reactive fixes, businesses can save time and money.
Benefits of Proactive Maintenance
Proactive maintenance involves regular inspections, routine servicing, and predictive measures to prevent equipment failure. This approach helps to identify potential issues before they lead to costly breakdowns, reducing unexpected downtime and extending the lifespan of machinery. Additionally, it creates a more predictable maintenance schedule, allowing for better planning and resource allocation.
Implementing a Proactive Maintenance Program
Establish a schedule for routine inspections and servicing to implement a proactive maintenance program. Use historical data and predictive analytics to anticipate when maintenance should be performed and ensure that your team adheres to this schedule rigorously. Consider developing a maintenance calendar that includes all necessary checks and services, and use tools that can automate reminders and alerts.
Utilizing Efficient Maintenance Software
Efficient maintenance software is a crucial tool for modern industrial maintenance. It allows plant managers to be flexible and mobile, streamlining various aspects of maintenance management.
Key Features of Maintenance Software
- Work Order Management: Efficient software helps create, track, and manage work orders seamlessly. This ensures that all maintenance tasks are documented and tracked from start to finish.
- Inventory and Parts Management: It keeps track of parts and inventory, ensuring that necessary components are available when needed. Automated reordering features can prevent stockouts and delays in maintenance.
- Asset History Logging: This logs the history of each asset, providing valuable data for future maintenance decisions. This historical data can help identify patterns and predict future maintenance needs.
- Accurate Data Collection: Collect and store data accurately, facilitating informed decision-making. Real-time data collection can provide insights into equipment performance and maintenance effectiveness.
- Custom Reports: Generate custom reports to monitor performance, identify trends, and make data-driven improvements. These reports can be tailored to specific metrics and KPIs relevant to your operations.
Clear Procedures and Documentation
Clear procedures and documentation are essential for maintaining consistency and quality in industrial maintenance.
Types of Documentation
- Checklists: Ensure all maintenance tasks are completed, and nothing is overlooked. Checklists provide a simple yet effective way to ensure thoroughness and consistency.
- Standard Operating Procedures (SOPs): Provide step-by-step instructions for performing maintenance tasks. SOPs help standardize processes and ensure all team members follow the same methods.
- Emergency Operating Procedures (EOPs): Outline the steps to take in emergencies. Having EOPs ensures that your team can respond quickly and effectively to unexpected issues.
- Guidelines: Offer general advice and best practices for maintaining equipment. Guidelines can cover many topics, from daily maintenance routines to long-term equipment care strategies.
Benefits of Clear Documentation
Clear documentation helps in training new staff, ensures consistency in maintenance practices, and reduces the risk of errors. It also serves as a reference guide for troubleshooting and decision-making.
Setting Clear Maintenance Goals
Setting clear maintenance goals helps to focus efforts and measure progress. These goals should be specific, measurable, achievable, relevant, and time-bound (SMART).
Examples of Maintenance Goals
- Reduce Downtime: Aim to reduce equipment downtime by a specific percentage. For example, you might set a goal to reduce downtime by 10% over the next year.
- Increase Equipment Lifespan: Set goals to extend the lifespan of key equipment. This could involve implementing new maintenance techniques or increasing the frequency of certain maintenance tasks.
- Improve Response Time: Establish targets for how quickly maintenance issues are addressed. Faster response times can reduce the impact of equipment failures on production.
Developing SMART Goals
To develop SMART goals, start by identifying the key areas of improvement within your maintenance operations. Set specific targets for each area, ensuring they are measurable and achievable. Align these goals with your overall business objectives to ensure they are relevant. Finally, set a timeline for achieving these goals and regularly review progress.
Measuring Processes Against Goals and Benchmarks
Regularly measuring your maintenance processes against established goals and benchmarks is crucial for continuous improvement.
Key Performance Indicators (KPIs)
- Mean Time Between Failures (MTBF): Measures the average time between equipment failures. A higher MTBF indicates more reliable equipment and effective maintenance practices.
- Mean Time to Repair (MTTR): Tracks the average time taken to repair equipment. Reducing MTTR can minimize the impact of failures on operations.
- Maintenance Compliance: Measures adherence to scheduled maintenance tasks. High compliance rates indicate that maintenance tasks are being performed as planned.
Using KPIs for Improvement
Analyze KPI data regularly to identify areas where performance is lacking. Use this data to decide where to focus your improvement efforts. Benchmark your performance against industry standards or similar operations to gauge your effectiveness.
With a proven history of success and diverse skills across the industry, Smith-Boughan’s industrial maintenance services utilize industry best practices to keep your operations operational.
Improving Processes to Meet Goals
Continuous improvement is a key aspect of effective industrial maintenance. Regularly review and refine your processes to ensure they are as efficient and effective as possible.
Steps for Process Improvement
- Analyze Data: Use data collected from maintenance software to identify areas for improvement. Look for trends and patterns that can reveal underlying issues.
- Gather Feedback: Solicit feedback from maintenance teams to identify pain points and areas for enhancement. Your team members often have valuable insights into what works and what doesn’t.
- Implement Changes: Make necessary adjustments to processes and procedures. Start with small, manageable changes and gradually scale up.
- Monitor Results: Track the impact of changes and adjust as needed to achieve desired outcomes. Use your KPIs to measure the effectiveness of the changes and ensure they are delivering the desired results.
Additional Best Practices for Industrial Maintenance
In addition to the practices mentioned above, here are some additional tips to enhance your industrial maintenance program.
Training and Development
Invest in the training and development of your maintenance team. Ensure they are well-versed in the latest maintenance techniques and technologies. Continuous learning helps them adapt to new challenges and improve overall maintenance efficiency.
Regular Audits and Inspections
Conduct regular audits and inspections to identify potential issues early. Audits help ensure compliance with maintenance schedules and identify areas for improvement.
Collaboration and Communication
Encourage collaboration and communication between different departments and teams. Effective communication ensures everyone is on the same page and working towards common goals. Regular meetings and updates can help share important information and address any issues promptly.
Use of Advanced Technologies
Leverage advanced technologies such as the Internet of Things (IoT), predictive analytics, and machine learning to enhance maintenance practices. These technologies can provide real-time insights, predict equipment failures, and optimize maintenance schedules.
Safety First
Always prioritize safety in all maintenance activities. Ensure that safety protocols are followed rigorously and that all team members are trained in safety procedures. A safe work environment not only protects employees but also ensures uninterrupted operations.
Elevate Your Industrial Maintenance Standards With Smith-Boughan
Improving industrial maintenance requires a combination of proactive strategies, efficient tools, clear documentation, and continuous improvement. Smith-Boughan provides expert maintenance solutions for industrial facilities, ensuring they’re safe, efficient, and productive. Our dedicated team helps you enhance your maintenance standards, reduce downtime, and extend the lifespan of your equipment.
Contact Smith-Boughan today to learn how we can help you achieve excellence in industrial maintenance.
Share This Post
More Like This
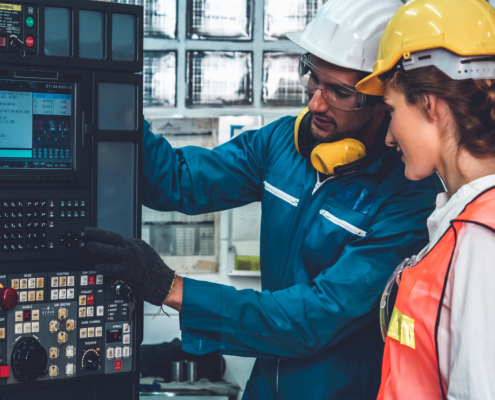
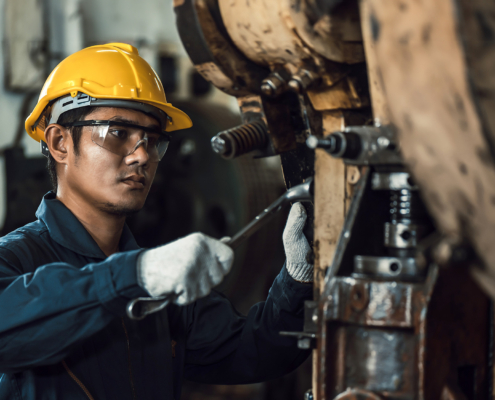
How to Develop a Quality Control Plan for Industrial Maintenance
Industrial Services (Quality Control), Maintenance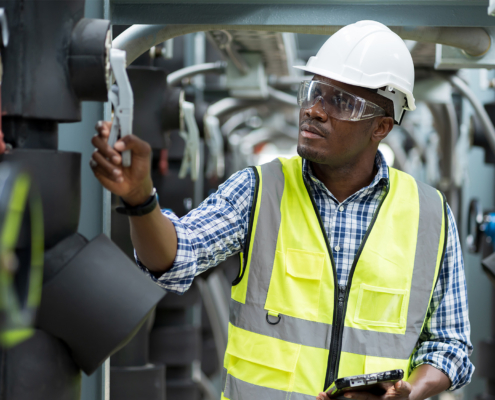
Understanding Industrial Maintenance Compliance Guidelines
Industrial Services (Maintenance), Maintenance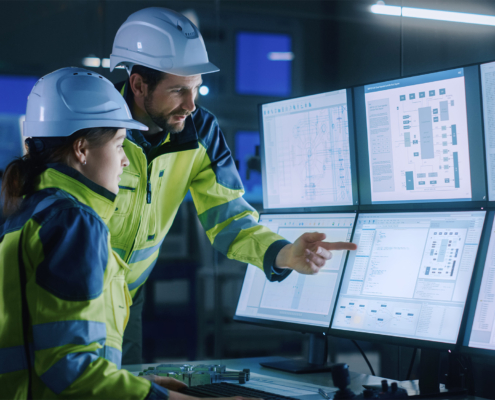
The Role of Technology in Industrial Maintenance Practice Innovations
Industrial Services (Maintenance), Maintenance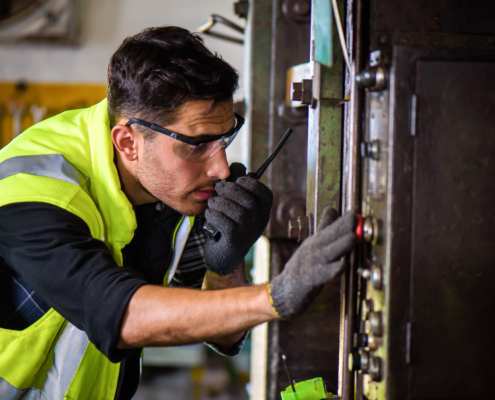
Factors to Consider When Choosing an Industrial Maintenance Provider
Industrial Services (Maintenance), Maintenance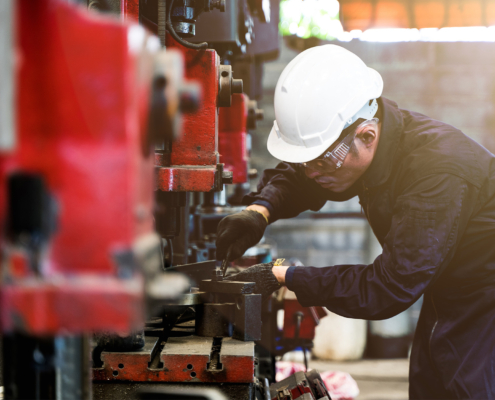
Exploring the Benefits of Routine Industrial Maintenance
Building Services (Maintenance Agreements), Maintenance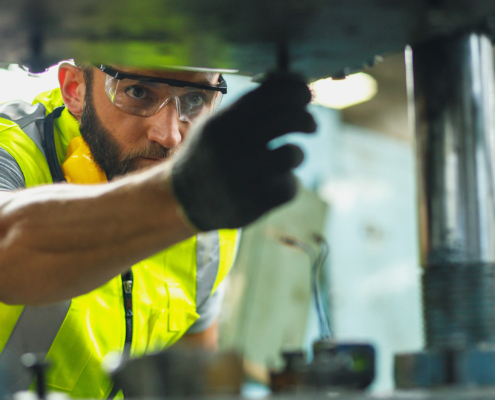
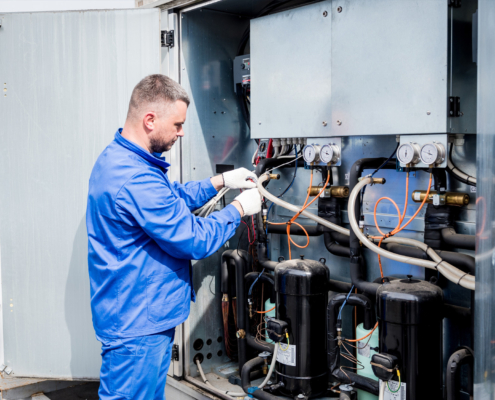
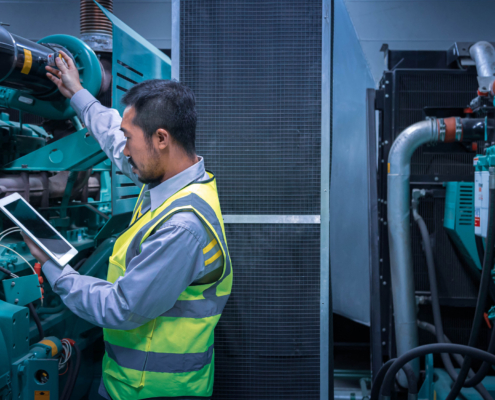
About Us
Smith-Boughan Mechanical has been servicing the Lima, Ohio, region with industry-leading mechanical design, fabrication, construction, and maintenance services since 1927.