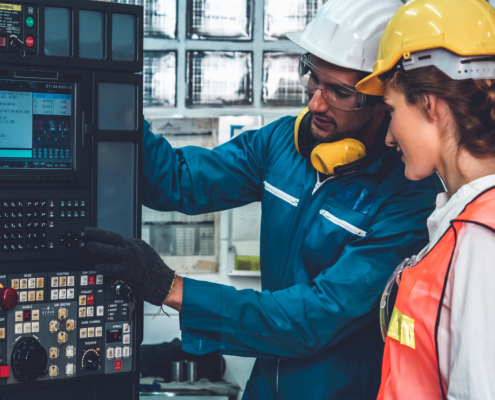
In modern industries, every component must function together flawlessly to achieve success. Planned maintenance is a key strategy that ensures this harmony by preventing breakdowns, maintaining efficiency, and extending asset life. However, its critical multi-phase process is often underestimated by many business leaders. This guide details the four vital phases of planned maintenance and the advantages it provides.
What Are the Four Phases of Planned Maintenance?
A planned maintenance program has four phases designed to identify and catch developing problems. These include:
Planning Phase: Identifying Maintenance Requirements and Developing Strategy
Before embarking on your maintenance journey, setting the map right is crucial. The planning phase, the first stage of planned maintenance, is all about diagnosis and strategy formulation. It begins with an extensive audit of your existing equipment, identifying what needs maintenance, and creating a thorough maintenance plan.
During this phase, maintenance managers conduct rigorous inspections to establish the present state of machinery, pinpoint maintenance tasks needed, and even project future repair needs. It’s a phase that determines the entire workflow of the planned maintenance strategy and sets the pace for the subsequent phases.
Key tasks in the planning phase include defining maintenance objectives, setting a priority level for each objective based on factors like risk potential and operational importance, setting aside resources such as labor and replacement parts, and finally leading to the creation of a comprehensive maintenance plan. A well-structured plan paves the way for the next step, which entails scheduling.
Scheduling Phase: Assigning Tasks and Determining Timelines
Upon creating a solid plan, the maintenance planner zooms into the finer details of allocating tasks and setting deadlines. The scheduling phase is akin to the lifeline of a planned maintenance system, determining the strategy’s tempo, rhythm, and rewarding results.
At this point, tasks are distributed among the maintenance technicians based on their area of expertise and availability. The task list and schedule should be clear enough for everyone, defining what needs to be done, the timeline, and who exactly is responsible for the task.
Defining timelines not only ensures the timely completion of work but also aids in avoiding task conflicts among the maintenance team. Equally important, proper scheduling allows maintenance work to be completed while minimizing interruptions to production activities.
Boosted efficiency, clear work orders, and heightened maintenance team morale are a few of the outcomes to expect from a well-scheduled maintenance phase. Next in line is the execution phase.
Executing Phase: Carrying Out the Planned Maintenance Tasks
With a reliable plan and a crisp schedule, the next step in the planned maintenance cycle is the execution phase. This is where the strategy and timelines meet the actual hands-on work. The maintenance tasks outlined in the maintenance plan are carried out according to the set schedule.
In this phase, maintenance technicians conduct the actual preventive maintenance, ranging from checks, cleaning, adjustments, testing, repairs, and minor replacements. The aim is to detect any floor anomalies quickly and resolve them before they result in significant machine breakdowns or safety hazards.
A key part of the execution phase is the documentation of maintenance activities. As the maintenance tasks are being completed, records are kept to monitor the progress and aid in the final phase, which is the process evaluation.
Evaluation Phase: Analysis of the Maintenance Process and Outcomes
The final point of the planned maintenance journey is the evaluation phase. Beyond being the conclusion, this phase serves as a fountain of enlightenment, providing invaluable insight into the effectiveness of maintenance activities and highlighting areas requiring improvement.
Here, completed maintenance tasks are reviewed extensively, using metrics such as downtime reduction, cost savings, and equipment lifespan extension to assess the efficacy of the planned maintenance strategy. Additionally, any observations made during the executing phase are critically examined, and lessons learned are used to refine the existing strategy, making it an ever-continuous improvement process.
Moreover, maintenance teams hold post-mortem meetings to study the process, identify any gaps, and determine ways to enhance future maintenance activities. The evaluation phase is a significant step in recognizing the triumphs and challenges of the planned maintenance system, allowing you to make an informed decision on the next step forward.
Smith-Boughan offers maintenance services that verify the operational capacity of all building components. Explore our services today.
What Are the Benefits of Planned Maintenance?
Planned maintenance offers several benefits for organizations in various industries. Some of the key advantages include:
Increased Equipment Reliability
Regular maintenance helps identify and address potential issues before they lead to equipment failures. This contributes to improved reliability and reduces the chances of unexpected breakdowns.
Extended Equipment Lifespan
By addressing wear and tear through planned maintenance, organizations can extend the lifespan of their equipment and assets. This can result in cost savings by reducing the need for premature replacements.
Cost Savings
Preventive maintenance can be more cost-effective than reactive maintenance. Fixing issues proactively can prevent larger, more expensive problems from arising, saving money in the long run.
Improved Safety
Regular inspections and maintenance activities enhance safety by identifying and addressing potential hazards. This is particularly important in industries where equipment failure or malfunction could lead to accidents or injuries.
Optimized Performance
Well-maintained equipment tends to operate more efficiently. Regular inspections and adjustments can optimize performance, improving productivity and reducing energy consumption.
Minimized Downtime
Scheduled maintenance allows organizations to plan and prepare downtime at times that are least disruptive to operations. This minimizes the impact on productivity compared to unexpected breakdowns.
Compliance With Regulations
Many industries have regulations and standards related to equipment maintenance. Planned maintenance helps organizations stay compliant with these regulations, avoiding legal issues and potential fines.
Improved Asset Management
Organizations can better track and manage their assets through planned maintenance programs. This includes keeping accurate records of maintenance activities, which can be valuable for inventory and financial management.
Enhanced Product Quality
In industries where equipment is crucial for production processes, planned maintenance can contribute to consistent product quality by ensuring that machinery operates at optimal levels.
Environmental Sustainability
Well-maintained equipment is often more energy-efficient, contributing to environmental sustainability goals by reducing energy consumption and minimizing the environmental impact of operations.
Consequences of Not Performing Planned Maintenance
The importance of prioritizing planned maintenance cannot be understated, especially when assessing the repercussions of its neglect. The decision to bypass consistent equipment care and treatment can invite a series of detrimental effects, such as equipment failure, production downtime, and safety hazards.
When unscheduled maintenance supersedes planned preventive maintenance, it signals the dominance of a reactive maintenance approach. This shift opens the door to sudden equipment failure. As problems are addressed only when they surface, there is an increased likelihood of abrupt breakdowns that adversely impact productivity and efficiency.
In addition to disrupting operations, equipment breakdown can initiate production downtime. Downtime not only halts the production cycle but also results in lost revenue. Prolonged downtime eats into operational hours, directly affecting output capacity and overall business profitability.
Prevent Equipment Breakdown With Our Planned Maintenance Program
Equipment issues are inevitable, but partnering with the right planned maintenance provider is key for preventing problems from impacting your operations. As a leading provider of mechanical solutions, Smith-Boughan offers industry-leading maintenance services that safeguard your HVAC and plumbing equipment and allow you to maximize the value of your investment.
Contact us today to learn more about our maintenance plans.
Share This Post
More Like This
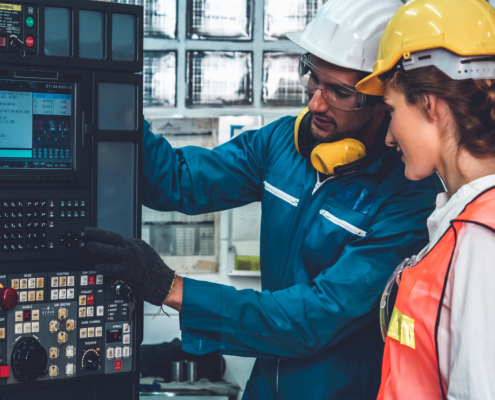
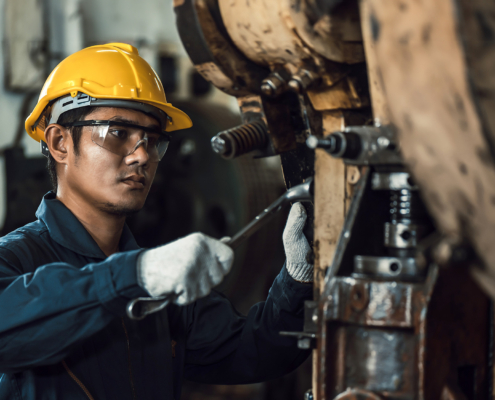
How to Develop a Quality Control Plan for Industrial Maintenance
Industrial Services (Quality Control), Maintenance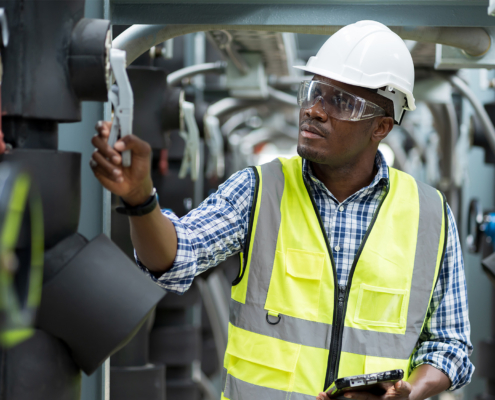
Understanding Industrial Maintenance Compliance Guidelines
Industrial Services (Maintenance), Maintenance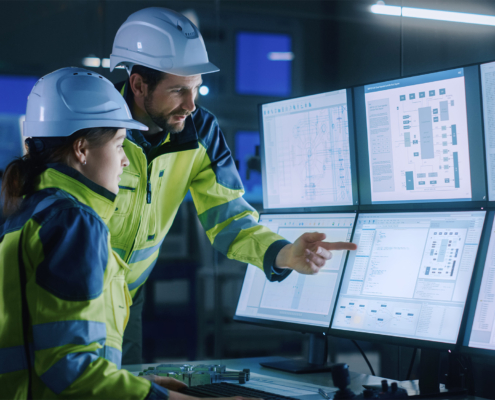
The Role of Technology in Industrial Maintenance Practice Innovations
Industrial Services (Maintenance), Maintenance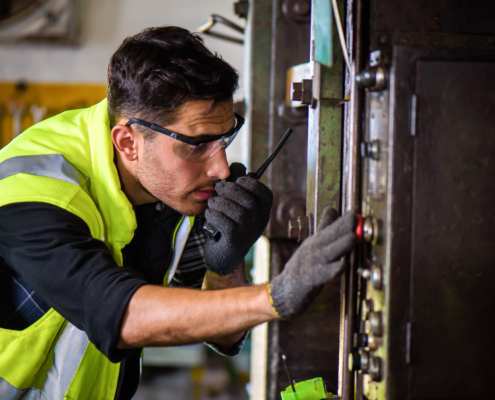
Factors to Consider When Choosing an Industrial Maintenance Provider
Industrial Services (Maintenance), Maintenance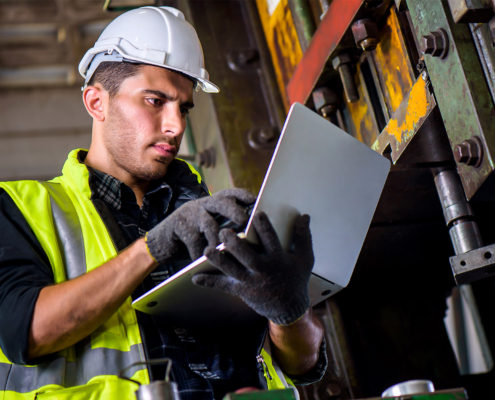
Best Practices for Improving Industrial Maintenance
Industrial Services (Maintenance), Maintenance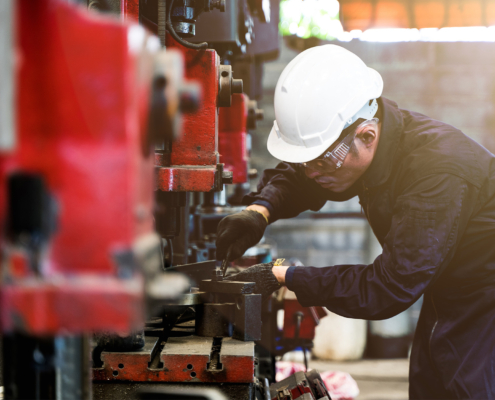
Exploring the Benefits of Routine Industrial Maintenance
Building Services (Maintenance Agreements), Maintenance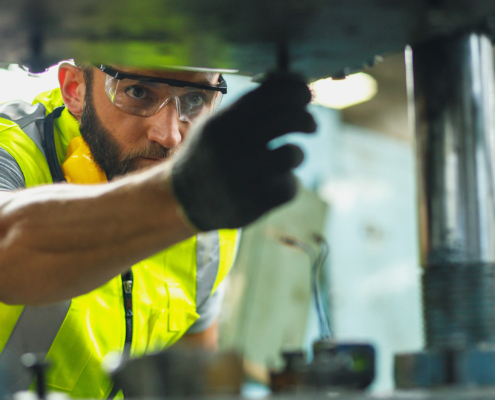
Your Guide to Industrial Maintenance
Building Services (Maintenance Agreements), Maintenance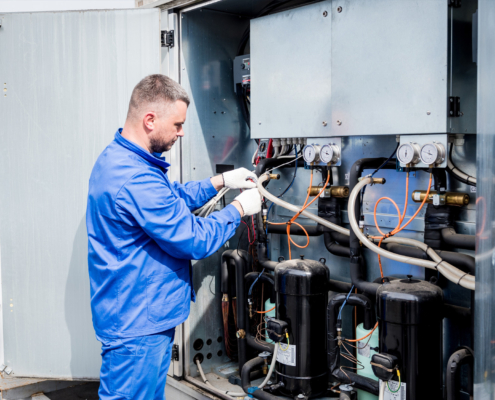
The Importance of a Commercial HVAC Maintenance Agreement
MaintenanceAbout Us
Smith-Boughan Mechanical has been servicing the Lima, Ohio, region with industry-leading mechanical design, fabrication, construction, and maintenance services since 1927.